Condition-based maintenance works on the premise that if it isn’t broken, don’t fix it. The idea behind this type of maintenance management, is that you carry out repair and maintenance work, only when needed. This ensures that machinery, equipment, systems, and spaces are fixed just in time before they turn into expensive repairs or replacements.
Handymen are like everyday superheroes who come to our help when we need a hand fixing things. With them around, we can keep our property safe and comfortable.
In this article, we will dive deeper into condition-based maintenance, its benefits, and key components. We will look at how it differs from predictive maintenance and how to identify assets that need this type of maintenance. We will also look at available tools and technologies that assist with condition-based maintenance. Finally, we’ll go through some of the key challenges and considerations when implementing it.
Step 1: Understanding the basics of condition-based maintenance.
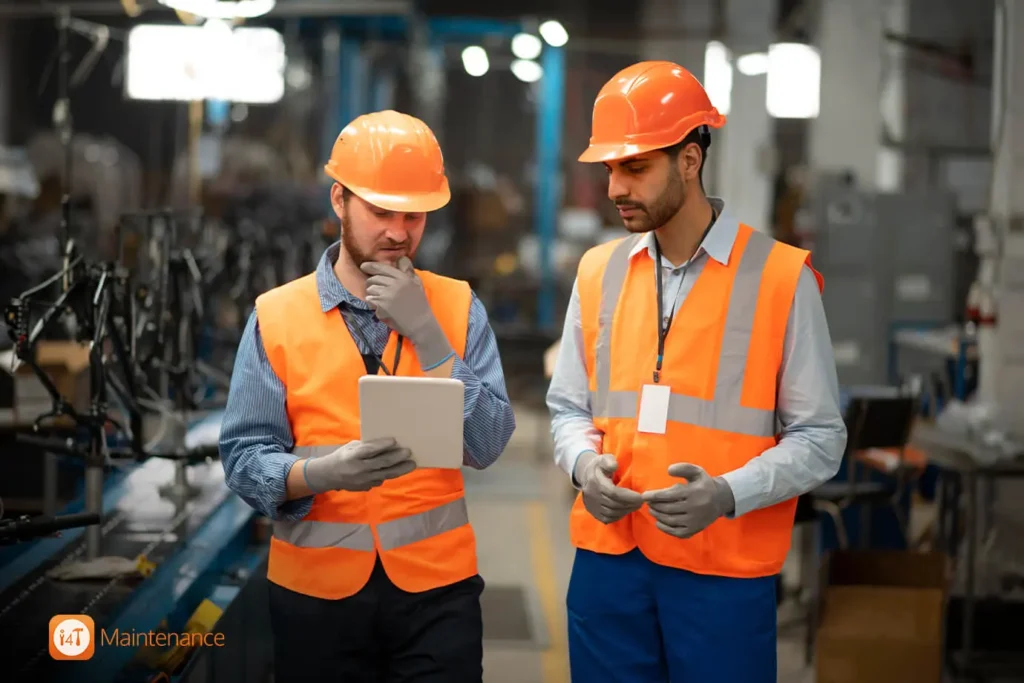
Before you implement CBM, it is important to understand what it entails.
What is condition-based maintenance?
Condition-based maintenance or CBM, is also called corrective maintenance. It uses sensors attached to equipment to identify potential deviations from the routine performance. Since these assets are monitored non-stop, action can be taken as soon as an issue is detected. This ensures maximum uptime without allocating resources to assets that are doing just fine.
Condition-based maintenance workflow
Different organizations use different techniques when it comes to CBM. However, in its simplest form, its workflow is as follows.
- Determine baseline standards
- Install sensors to monitor conditions
- Collect and monitor data
- Identify deviation from base-line standards
- Create a corrective action work order
- Perform corrective maintenance
Benefits of condition-based maintenance
When chosen for the suitable asset type, CBM offers multiple benefits:
Saves time and money: It doesn’t allocate a maintenance budget to machines that are doing just fine. Hence, it saves money on unnecessary maintenance work.
Reduces downtime: It identifies issues as soon as they arise. Hence immediate corrective maintenance minimizes downtime.
Extends machine life: It catches and fixes issues before they turn into bigger problems. Hence, condition-based maintenance, helps assets stay healthier for longer.
Components of condition-based maintenance
Condition-based maintenance is comprised of 4 key components, contributing towards, data acquisition, analysis, and decision making.
These components are:
Sensors: These are small devices attached to the machines, telling us about their health. They can sense changes in temperature, vibration, and sound. These changes catch baseline deviations telling us something may be wrong.
Data analysis: The information sensors send our way, needs to be understood. That is where data analysis kicks in. It’s like putting the pieces of the puzzle together.
Maintenance team: Once we know what the problem is, we need to create a work order and assign it to a technician.
Communication tools: This keeps everyone on the same page regarding asset health. From alerting about a potential fault to notifying about a new work order, communication plays a vital role here.
Step 2: Access and identify critical assets
Not all assets in your facility, factory, or building are critical assets. Critical assets disrupt your entire operations in case they malfunction or break down. For condition-based maintenance to be truly cost-effective, we need to identify these assets. Once that is done, we need to prioritize them for maintenance.
How to determine critical assets
When deciding which items are most critical to your business, look at the following:
Role in operations: If an asset plays a major role in ensuring smooth operations of your business, it is critical.
Replacement cost: If an asset is high-cost, replacing it will be a major expense. Hence is considered a critical asset.
Safety concerns: If a malfunctioning asset can become a safety hazard, it is a critical asset.
History of breakdowns: If an asset has broken down a lot in the past, it might happen in the future as well. This makes it a critical asset and needs attention.
How to carry out asset evaluation
These methods can be used to determine if an asset is critical or not.
Inspection checklist: This includes going through each machine and determining if it meets the critical criteria.
Software systems: This includes keeping a digital record of all assets, their roles, costs, and breakdown histories. Based on this the software can determine if they are critical or not.
Expert opinion: Sometimes the best way is to ask the people who use these assets regularly. Their input can help determine if these assets are critical or not.
How to prioritize assets for condition-based maintenance
Managers can prioritize maintenance work based on the information gathered above.
You can use a matrix to give a score to each asset based on different factors. These include its role, consequences of failure, breakdown history, replacement cost, and age of the asset.
Assets having the highest score or those falling in the most critical quadrant, need the most attention.
Step 3: Choose the right monitoring tools and technologies
Condition-based maintenance uses a wide range of tools and technologies to keep a close eye on the assets we need to monitor.
Types of monitoring tools available
Some of the most common ones include:
Vibration analysis: This looks at a change between how a machine was vibrating before vs. now to alert if something is not right.
Thermal imaging: This tool captures images of parts of a machine that get too hot while running.
Ultrasound: This technique can identify the sound of tiny leaks or cracks in the machinery, to report them on time.
Oil analysis: The looks at lubricants used by a machine to determine its overall health and detect potential issues.
Motor current analysis: This analyzes the current in machines and spots any change to hint any issues with its performance.
Factors to consider when selecting monitoring tools
Monitoring tools work best when they are used for the asset they are intended for. When selecting monitoring tools also consider their cost, ease of use, precision, and the environment the machine is located in.
Integrating monitoring tools with existing systems
When picking new tools, it’s important to make sure they are compatible with your existing systems. The system you use should be able to offer a centralized dashboard to see all your data in one place.
Consider training your team to use the new tools and understand how integration with your current system works. Finally, think about where all of this data will be stored for easy access and analysis.
Step 4: Establish monitoring protocols and thresholds
Defining baseline measurement tells us what is the state of our assets when they are healthy or perfect. Without the information on how they behave when everything is right, we cannot spot when something goes wrong.
Setting up the baseline and acceptable limits
To set up the baseline, we need to record data like temperature, vibration, and sounds under normal conditions.
Next, we need to determine the threshold. This is the acceptable limit for each asset to which it can deviate from the baseline.
When setting the threshold, consider factors such as the machine’s role, its environment, and any recommendations from the manufacturer. For example, if a machine goes above the acceptable temperature threshold in an already hot room, then it’s probably natural for it to do so. This will not be treated as an alert warranting condition-based maintenance.
It’s important to note that you must regularly update the baselines and thresholds. As the machine ages or maintenance work is performed on it, your definition of ‘normal’ should also change.
Importance of continuous monitoring and data analysis
Monitoring your assets’ health is vital to their performance. This helps spot issues early on before they turn into expensive repairs or replacements.
The more data your monitoring tools can collect over time, the more accurate will be your analysis, and the more precise your maintenance plan will be.
With this data in hand, you can make smart decisions as to which assets need maintenance, when they need it and where can costs be saved.
Step 5: Train maintenance teams and implement CBM
Before you hand over the condition-based maintenance tools and software to your team, you need to train them first. Make sure they understand how to spot issues and analyze and interpret the data that the devices collect.
Your team of technicians also needs to be trained on how to work safely around a machine that is showing signs of a problem.
Best practices for training maintenance teams
Hands-on learning: Provide practical demonstrations to the team and opportunities to practice with the tools.
Regular refresher courses: Technologies evolve and your team needs to be updated regularly to work with new tools that you have introduced.
Feedback loop: Make sure to ask your team about their experience and any challenges they are facing with the tools, the software, or the implementation process.
Use real-life scenarios: Allow them to practice with real scenarios to make their learning relatable.
Best practices for implementation of condition-based maintenance
Pilot program: Consider starting with a few assets at a time. Let your team test the approach and learn before full-fledged implementation.
Review and adjust: After the pilot, gather feedback from the team. Review what worked, what failed, what challenges came up, and what necessary adjustments you need to make.
Full implementation: Once you have seen the positive impact of the pilot program and you are confident to go full-fledge, you can implement the new approach across the board.
Continuous improvement: CBM is not a set-and-forget approach. Regularly access the process, the tools, and training, to ensure your approach remains relevant and current.
Challenges when implementing condition-based maintenance
Despite its effectiveness, condition-based maintenance has its challenges. These include:
Initial investment cost: Implementing CBM requires investing in new tools, technology, training, and personnel. These costs can be significant for small businesses. Fewer breakdowns and reduced downtime can offset these costs.
Resistance to change: Employees used to traditional methods of maintenance management may find the new approach daunting. Involve them in the decision-making process and provide training to fill the skill gap.
Data overload: The amount of data CBM systems can collect can be too overwhelming to draw meaningful insights. Invest in software that can provide data analytics. Look for features like organizing and filtering options, that can help you narrow down information.
Integration with existing systems: If your new tool is not able to talk with existing systems used by your organization it can become a hurdle during the implementation process. Do your homework during the selection process. Look for systems that offer seamless integration capabilities.
Reliability of sensors and tools: If your tools are inaccurate or not suitable for the intended asset, they can provide misleading data. This can lead to incorrect maintenance decisions. Invest in high-quality sensors and regularly test them for accuracy.
Conclusion
Condition-based maintenance is a data-driven approach to improving the reliability of your assets.
Its implementation requires a thorough understanding of the process. You need to identify critical assets and invest in the right tools. You will also need to set the monitoring baseline and thoroughly train your teams before the implementation.
i4T Maintenance is a maintenance management platform, that offers to fast-track and streamline your maintenance processes. We cater to the property, construction, and services sectors.
You can learn more about our solution, by booking a demo.
FAQs
CBM is a maintenance strategy where equipment is serviced based on its actual condition. It is determined through monitoring and diagnostic tools, rather than on a set schedule.
Traditional maintenance follows a set schedule regardless of equipment condition. CBM, on the other hand, only performs maintenance when there’s an actual need. This helps save time, money, and resources on unnecessary repairs.
Common tools include vibration analysis, thermal imaging, ultrasound, oil analysis, and motor current analysis, among others.
CBM can lead to reduced downtime, longer equipment lifespan, cost savings, and improved safety by addressing issues before they become critical.
Yes, challenges can include initial investment costs, resistance to change, data overload, skill gaps, and ensuring the reliability of monitoring tools.