Maintenance management for SMEs in Australia is vital to keeping the building running smoothly. Whether it’s machinery, office equipment, or company vehicles, regular maintenance is key to avoiding unexpected breakdowns and keeping everything on track. Good maintenance doesn’t just prevent costly repairs, it also boosts productivity and keeps workplaces safe.
But for many SMEs, balancing tight budgets with proper maintenance can be tough. With limited funds and small teams, it’s tempting to delay maintenance to save money. Unfortunately, this often leads to bigger, more expensive problems down the line. Many businesses also struggle with finding the right tools or expertise to manage maintenance efficiently.
This blog is here to help! We’ll share simple, affordable strategies, including the use of property maintenance management software, that make it easier to take care of your business’s assets without breaking the bank.
By being proactive and organised, SMEs can save money, reduce stress, and keep everything running like clockwork.
Importance of Effective Maintenance for SMEs
For small to medium businesses (SMEs), regular maintenance is a simple but powerful way to keep everything running smoothly. It helps avoid costly problems, boosts efficiency, and ensures a safer workplace.
Save Money on Repairs
Fixing small issues early is much cheaper than dealing with major breakdowns. Regular maintenance prevents small problems from turning into expensive repairs or replacements.
Increase Productivity
When equipment works well, your team can work without interruptions. This means less downtime, smoother operations, and more work getting done on time.
Keep Everyone Safe
Faulty equipment can be dangerous. Regular checks and repairs make sure your workplace stays safe for everyone, reducing accidents and other risks.
Make Equipment Last Longer
Taking care of your assets helps them last longer. Well-maintained tools, machines, and vehicles don’t wear out as quickly, saving you money on replacements.
Avoid Unplanned Downtime
Surprise equipment failures can cause big delays. Regular maintenance reduces the chances of unexpected breakdowns, keeping your business on track.
By making maintenance a priority, SMEs can save money, work more efficiently, and create a safer, more reliable workplace.
Key Cost-Effective Maintenance Strategiese
For small to medium businesses (SMEs), property maintenance management software is a game-changer when it comes to keeping operations smooth and costs under control. By combining this technology with smart strategies, SMEs can take care of their equipment and facilities without overspending. Let’s explore these strategies in more detail.
Preventive Maintenance
Preventive maintenance focuses on regular care to stop small issues from becoming big problems. It’s like giving your car regular oil changes to avoid a costly engine repair.
Why It’s Important:
Preventive maintenance saves money by reducing emergency repairs and minimising downtime.
It helps assets last longer, so you don’t need to replace them as often.
A well-maintained workplace is safer for employees and customers.
How to Create a Preventive Maintenance Schedule:
List all equipment:
Start by identifying what needs regular maintenance, such as HVAC systems, machinery, or office equipment.
Set regular intervals: Use manufacturer recommendations or monitor how often the equipment is used.
Use property maintenance software: Tools like CMMS (Computerised Maintenance Management Systems) can automate scheduling and send reminders.
Review and adjust: Over time, refine your schedule based on patterns or recurring issues.
Use of Technology for Maintenance Management
Property maintenance management software helps businesses stay on top of their maintenance tasks. It reduces human error and ensures nothing is forgotten.
Affordable Software for SMEs:
Options like i4T Maintenance offer solutions for small businesses as well as large enterprises. They’re easy to use and budget-friendly.
How It Helps:
Create Work Orders: Turn tenant and owner service requests into work orders in a snap and find the best supplier to do it for them.
Schedules tasks automatically: Let your suppliers know about recurring maintenance, and they’ll schedule it in their calendar, so you don’t have to fret when it’s time for maintenance.
Tracks progress: Ensure all work is carried out as per requirements and keep a record for audit.
Saves time: No need for manual spreadsheets or sticky notes. Everything is streamlined.
Outsource Specialised Services When Needed
Some tasks require specialised skills or equipment that your team doesn’t have. In these cases, outsourcing can save money and ensure the job is done right.
When Outsourcing Makes Sense:
For tasks like HVAC repairs, electrical work, or advanced machinery servicing.
When the cost of training or buying tools is higher than hiring an expert.
How to Get the Best Results:
Choose reliable providers: Look for companies with good reviews, certifications, and proven experience.
Compare costs: Get multiple quotes to ensure you’re not overpaying.
Set clear expectations: Write a contract that defines what’s included, timelines, and costs.
When to Keep it In-House:
Simple, routine tasks like cleaning, basic inspections, or lubrication can often be handled by your team with minimal training.
Train Staff for Basic Maintenance
Your team can handle small issues quickly and effectively with the right training. This reduces reliance on external contractors and saves money.
Why It’s Valuable:
Employees can fix minor problems on the spot, preventing them from turning into major ones.
It reduces downtime since there’s no waiting for outside help.
How to Train Your Team:
Start with basics: Teach employees how to spot wear and tear, clean equipment, and handle simple repairs.
Provide easy resources: Create checklists or videos for common tasks.
Ongoing learning: Offer occasional workshops or refresher sessions to keep skills sharp.
Cross-Training Benefits:
Employees can step in for each other during absences.
A versatile team is more prepared for unexpected situations.
Inventory Control and Spare Parts Management
Managing spare parts effectively prevents unnecessary spending and avoids delays when something needs fixing.
Why It’s Important:
Overstocking parts ties up money and space while running out of key parts can lead to downtime.
How to Stay Organised:
Use inventory tracking tools: Many property maintenance software systems include inventory management features.
Track frequently used parts: Keep records of which parts are replaced often and ensure you always have them on hand.
Set reorder levels: Automate reorders when stock reaches a minimum level.
Store parts properly: Organise parts in labeled containers to save time and prevent loss.
Cutting Costs:
Work with suppliers to negotiate better prices for bulk orders on commonly used parts.
Consider sharing rare or expensive parts with neighboring businesses.
Implement Condition-Based Monitoring (CBM)
Condition-Based Monitoring (CBM) uses real-time data from sensors to monitor equipment. It lets you know when maintenance is needed, rather than sticking to a fixed schedule.
Why It’s Useful:
You don’t waste time or money maintaining equipment that’s still in good condition.
CBM detects problems early before they cause breakdowns.
How to Get Started:
Install affordable sensors to track things like temperature, pressure, or vibration.
Use portable devices if installing sensors isn’t an option.
Pair CBM tools with maintenance software to get alerts when something’s wrong.
Energy Efficiency and Sustainability Measures
Sustainable maintenance practices can save money and make your business more environmentally friendly.
Simple Steps for Sustainability:
Energy audits: Identify areas where energy is being wasted, such as old lighting systems or inefficient HVAC units.
Regular servicing: Keep equipment running efficiently to use less energy and reduce wear.
Upgrade where possible: Replace outdated systems with energy-efficient models to save on utility bills.
Long-Term Benefits:
Lower energy bills free up funds for other business needs.
You may qualify for government rebates or incentives for adopting green technologies.
By following these strategies and using property maintenance management software, SMEs can reduce costs, improve efficiency, and keep operations running smoothly.
With a little planning and the right tools, effective maintenance can be affordable and stress-free.
Financial Planning for Maintenance
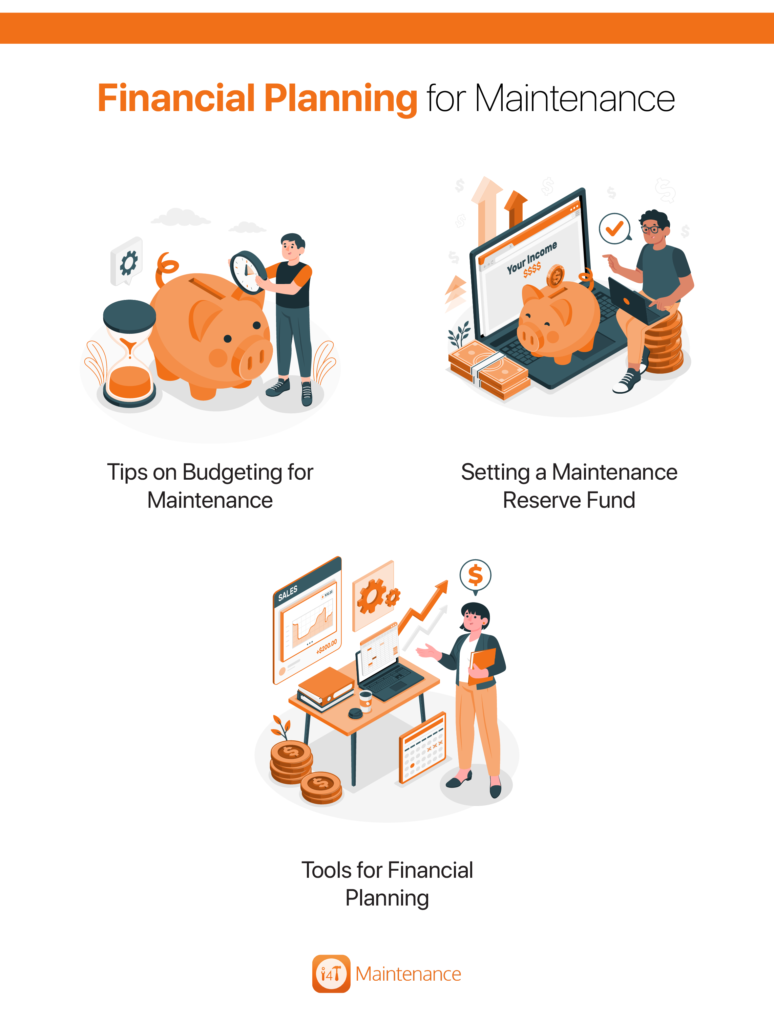
Financial planning is crucial for SMEs to manage maintenance costs effectively. Without a plan, these expenses can strain your budget and disrupt other business priorities. Here’s how to stay on track and handle unexpected costs.
Tips on Budgeting for Maintenance
- Review Past Costs: Look at previous repair and servicing expenses to predict future needs. Spot trends like seasonal spikes or recurring issues.
- Plan Preventive Maintenance: Budget for routine checks and small fixes to avoid bigger, costlier problems later. Use property maintenance software for accurate cost estimates.
- Think Long-Term: Set aside funds for major repairs, replacements, or upgrades to energy-efficient equipment to save in the future.
- Separate Fixed and Variable Costs: List predictable expenses (e.g., service contracts) and flexible costs (e.g., unexpected repairs) to budget more accurately.
Setting a Maintenance Reserve Fund
Even with a budget, surprises happen. A reserve fund acts as a safety net to handle unplanned expenses.
- Why It’s Important: Covers emergencies without disrupting your budget and avoids further delays or damage.
- How to Build It:
- Save 10–15% of your annual maintenance budget.
- Add small amounts monthly to make saving easier.
- Keep it in a dedicated account to avoid using it for other needs.
- Replenish It: If you use it, rebuild the fund quickly to stay prepared.
Tools for Financial Planning
- Property Maintenance Software: Tracks expenses, forecasts costs, and finds areas to save.
- Spreadsheets or Apps: Simple tools for smaller businesses to allocate funds and monitor spending easily.
With a clear budget and a reserve fund, SMEs can handle both routine maintenance and unexpected challenges without financial strain. Planning keeps your business running smoothly.
Measuring Success: Key Maintenance KPIs for SMEs
Tracking the right Key Performance Indicators (KPIs) helps small to medium businesses (SMEs) understand how well their maintenance strategies are working. These metrics highlight what’s going well, where to improve, and how to make the most of your maintenance efforts. Here are the key KPIs to monitor and how they help.
Key Maintenance KPIs for SMEs
- Equipment Downtime
- What It Tracks: How much time equipment is not working?
- Why It Matters: Less downtime means better productivity. It helps you spot problem equipment and improve maintenance schedules.
- Cost Savings
- What It Tracks: Money saved by using better maintenance strategies.
- Why It Matters: Shows if preventive maintenance and cost-cutting efforts are working.
- Response Time
- What It Tracks: How quickly maintenance issues are addressed and fixed.
- Why It Matters: Faster responses prevent bigger problems and reduce disruptions.
- Mean Time Between Failures (MTBF)
- What It Tracks: The average time equipment works without breaking down.
- Why It Matters: Higher MTBF means your assets are reliable and well-maintained.
- Mean Time to Repair (MTTR)
- What It Tracks: How long it takes to complete a repair.
- Why It Matters: Shorter repair times mean your team is efficient and well-prepared.
- Work Order Completion Rate
- What It Tracks: How many maintenance tasks are completed on time?
- Why It Matters: High rates show your maintenance is organised and on track.
- Spare Parts Inventory Turnover
- What It Tracks: How often spare parts are used and restocked?
- Why It Matters: Prevents overstocking or running out of critical parts, keeping equipment running smoothly.
How Tracking KPIs Helps
- Spot Issues: Downtime or MTBF can show which equipment needs attention.
- Improve Maintenance: Analysing trends helps adjust schedules and prioritise tasks.
- Save Money: Cost-saving KPIs show where you’re cutting expenses effectively.
- Boost Productivity: Faster response times and more completed tasks mean fewer disruptions.
- Plan Ahead: Regularly reviewing KPIs helps refine your strategies and meet business goals.
Monitoring these KPIs makes maintenance easier to manage and more effective. With clear data, SMEs can reduce costs, improve efficiency, and keep operations running smoothly.
Real-World Examples of Cost-Effective Maintenance for Australian SMEs
Here are some examples of how Australian SMEs have successfully implemented cost-effective maintenance strategies to save money and improve efficiency.
1. Optimising Preventive Maintenance Tasks
An Australian SME reviewed its preventive maintenance (PM) processes to find cost-saving opportunities. By analysing each task, the company removed or adjusted unnecessary maintenance routines without risking equipment reliability.
- Results:
- Saved 2.62% on annual maintenance costs.
- Reduced maintenance labour hours by 2.38%, saving the equivalent of six full-time employees.
- Key Takeaway: Streamlining maintenance schedules can save money and time.
Source: Covaris
2.Condition-Based Monitoring in Manufacturing
Australian manufacturing SMEs introduced condition-based monitoring (CBM) with affordable sensors to track the health of their equipment. CBM alerts businesses to potential issues before failures occur.
- Results:
- Reduced unexpected downtime.
- Extended equipment lifespan.
- Lowered overall maintenance expenses.
- Key Takeaway: Using low-cost monitoring devices can help SMEs maintain assets without overspending.
Source: MDPI
These examples show how simple strategies, like optimising maintenance schedules, adopting predictive tools, and using affordable monitoring systems, can help SMEs save money and improve efficiency.
With the right approach, even smaller businesses can achieve big results in maintenance management.
Conclusion
Managing maintenance on a budget is achievable for small to medium businesses (SMEs) with the right strategies in place. By focusing on cost-effective approaches, businesses can save money, reduce downtime, and keep operations running efficiently.
Preventive maintenance is a game-changer, as it helps avoid expensive repairs and extends the life of equipment. Using property maintenance management software simplifies scheduling, tracking, and organising maintenance tasks, making it easier to stay on top of responsibilities. Training staff to handle basic maintenance tasks, managing spare parts effectively, and adopting condition-based monitoring are also smart ways to keep costs low.
One of the most important steps is being proactive. Fixing small issues before they grow into big problems can save both time and money. Setting aside a maintenance reserve fund ensures that your business is prepared for unexpected expenses. Tracking Key Performance Indicators (KPIs), like downtime and cost savings, allows you to measure success and improve over time.
By taking an organised approach to maintenance and using affordable tools, SMEs can optimise performance while keeping costs under control. Investing in maintenance isn’t just about avoiding problems; it’s about building a strong, reliable foundation for your business to grow.
Start today with i4T Maintenance Property Maintenance Management Software, and see the difference a proactive approach can make! Book a demo today.
FAQs
Preventive maintenance is one of the best strategies, as it helps avoid costly breakdowns and extends the life of equipment.
It simplifies scheduling, tracks tasks, manages spare parts, and provides insights to optimise maintenance processes.
A reserve fund covers unexpected repairs, preventing financial strain and ensuring quick fixes when issues arise.
A CMMS lets you create tasks and assign them to team members. It tracks what’s being worked on and helps make sure jobs get done when they’re supposed to.
Key KPIs include equipment downtime, cost savings, response times, MTBF (Mean Time Between Failures), and work order completion rates
Yes, training staff for basic tasks reduces reliance on external contractors and helps fix small issues quickly.