Templates
Repair & Maintenance Work Order
Template
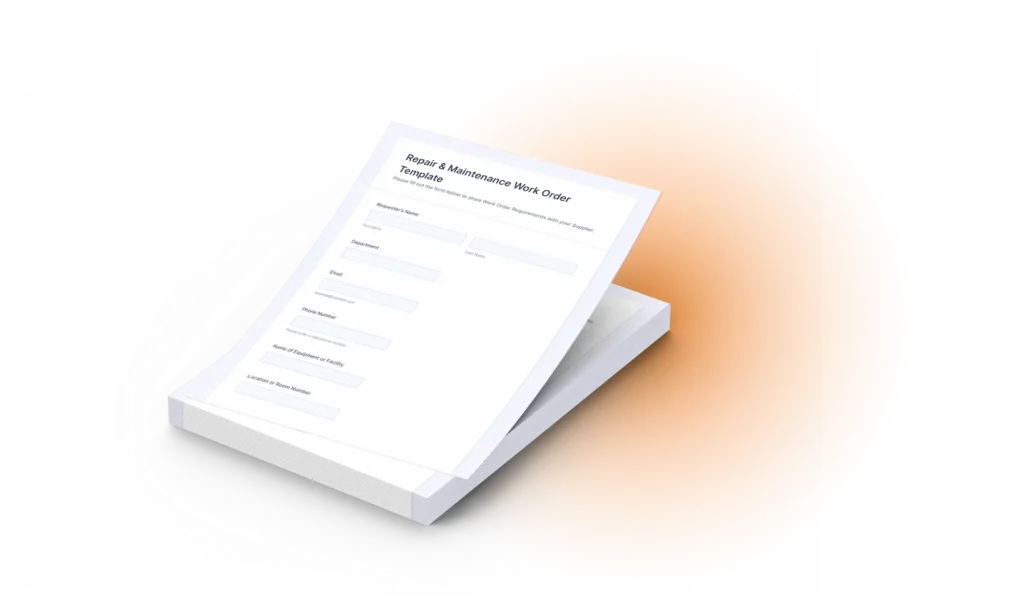
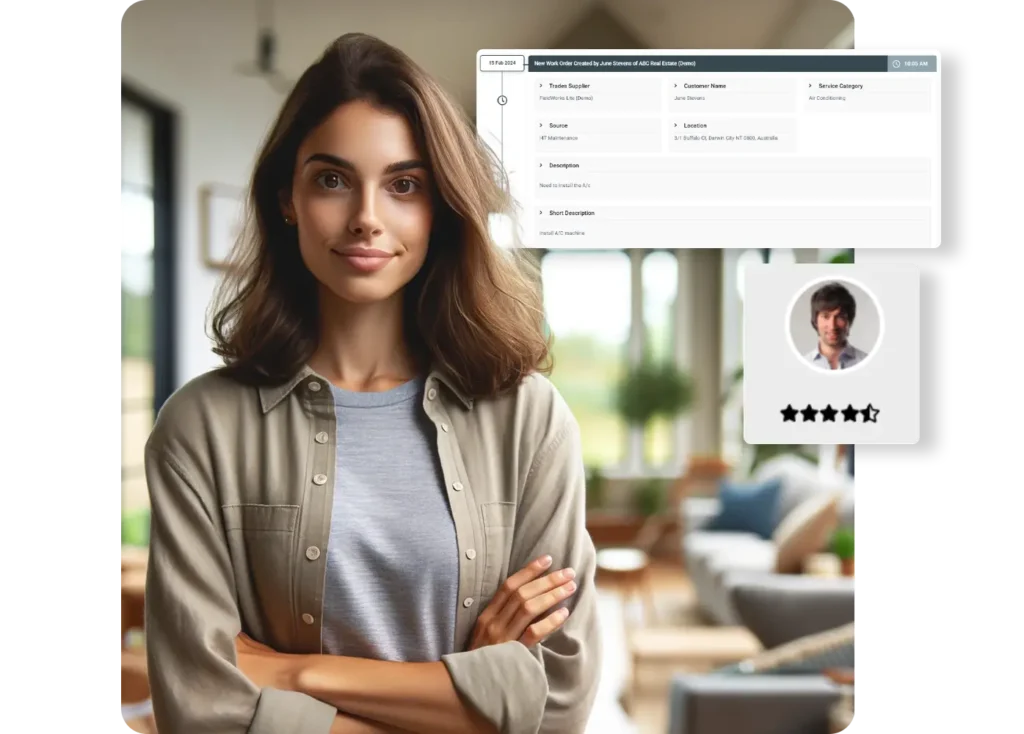
Enhance Your Workflow with i4T Maintenance Management Software
- Receive Maintenance Requests
- Automate Work Order Management
- Manage Supplier Quote Requests
- Manage Supplier Compliance
- Track Work Order Progress
- Manage Tenant Feedback
Other Business Tools You Should Try
- Business Plan Template
- Invoice Creation Tool
FAQs
To get the most out of your work orders make sure you follow these best practices:
- Include as much detail as possible to avoid misunderstandings.
- Assign priority levels (e.g., low, medium, high) based on urgency.
- Record location, equipment ID, and the nature of the problem clearly.
- Use a consistent template to make data easier to interpret and analyse.
- Allocate tasks to technicians based on their skills, workload, and compliances.
- Combine reactive and preventative work orders to improve long-term efficiency.
As a maintenance manager, you will be required to create several work orders for property and asset maintenance. The type of maintenance work order you create can vary from asset to asset, industry standards, and your company’s specific requirements.
Following are the different types of work orders you can assign to your team.
- Reactive Maintenance Work Orders: Address unplanned issues like equipment breakdowns or urgent repairs.
- Preventative Maintenance Work Orders: Scheduled tasks aimed at preventing failures, such as routine inspections or filter changes.
- Predictive Maintenance Work Orders: Tasks based on condition monitoring data, such as vibration analysis or temperature readings.
- Corrective Maintenance Work Orders: Repairs identified during inspections that are not yet urgent but need attention.
- Emergency Work Orders: High-priority repairs required to address safety or operational risks immediately.
- General Maintenance Work Orders: Routine upkeep tasks like cleaning, painting, or landscaping.
Inspection Work Orders: Scheduled evaluations of equipment or facilities to ensure compliance and identify potential issues.
A work order management system keeps all your maintenance tasks organised, ensures faster response times, reduces errors, and improves communication between teams.
It helps track resources, maintain records, scale with growing demands, and transition to preventative maintenance. Plus, it provides insights to make better decisions.
For complete and efficient work order management, try i4T Maintenance.